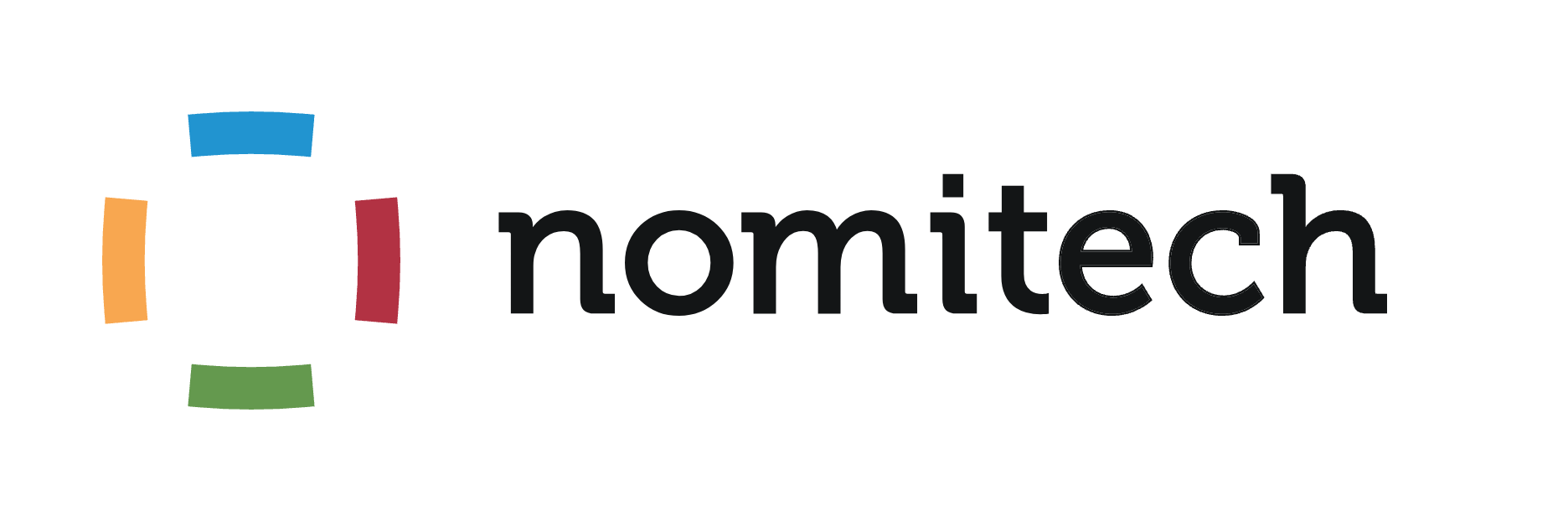
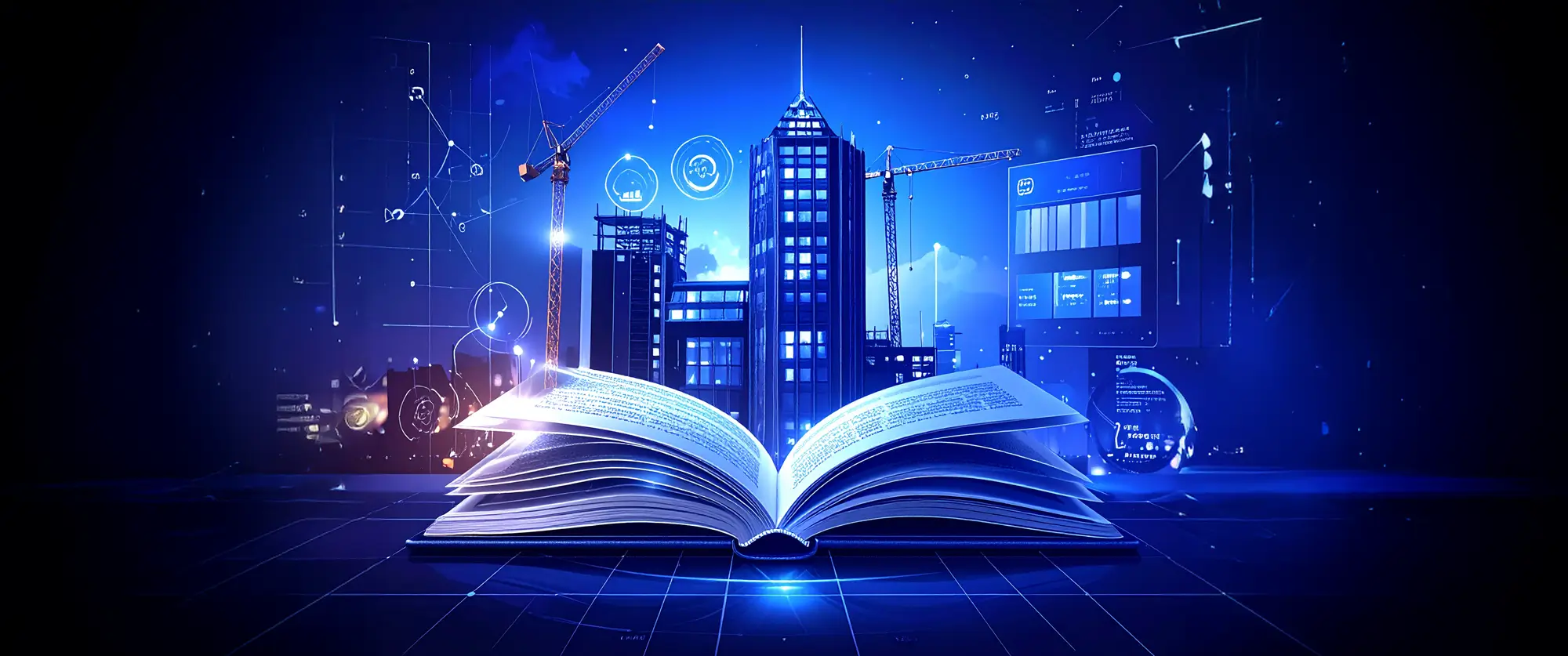
Cost Estimating in Construction: Methods, Tools, and Best Practices
TL;DR: Construction cost forecasting is the backbone of project success, powering smart budgeting, trust among stakeholders, and ongoing risk control. This guide unpacks core estimate types, practical step-by-step methods, and why technology, like CostOS and CellBIM, matters more than ever for accuracy and teamwork. Dive in to strengthen your estimating process and start your projects off on the right financial foot.
Introduction to Cost Estimating in Construction
Good cost estimation in construction is vital for any new construction project. It’s more than a spreadsheet exercise.
Accurate construction cost estimation helps define a project's scope, resources needed, time frame, and budget. The sooner you start to estimate construction costs, the better. Early estimates set direction and lay the foundation for success, ideally beginning during the project’s conceptual or idea phase.
Why Cost Estimating Matters in Construction
The Importance of Accurate Construction Cost Estimation
If you’ve ever watched building costs slip away or missed out on a project because your bid was off, you know just how critical a robust cost estimate is.
Too many teams in the construction industry lose money or momentum, not for lack of expertise, but because their construction cost forecasts can’t keep up when the details change or the data is scattered.
In a world where every number is scrutinized and profit margins get thinner each year, getting your construction cost estimating process right is non-negotiable.
Clients, investors, and project partners want construction estimates they can rely on, and they want them quickly. If your estimate construction costs show up late, look shaky, or are not rooted in real data, you’re opening the doors to unexpected costs and financial risks. It’s this environment that’s driving construction cost estimators to improve their processes and use advanced estimating tools
Establishing Realistic Budgets and Feasibility
A clear and accurate expense estimate anchors your budget. It keeps construction projects grounded in reality and prevents costly missteps.
Accurate construction cost estimation enables project managers to identify potential risks, create realistic timelines, and develop contingency plans. As DG Jones & Partners notes, estimates built on solid specs and plans lead to approvals and smoother execution.
Estimators require input from architects and engineers to ensure a project is financially feasible and meets scope requirements. Without a clear sense of project expenses, it becomes difficult to provide an accurate cost estimate.
Well-researched numbers give decision-makers the facts they need. The Constructor illustrates how reliable cost estimation supports every subsequent planning decision and enables strong project planning.
Grounded estimates allow you to:
- Allocate resources and materials efficiently, optimizing project costs
- Spot savings and alternatives before choices become costly
- Identify and manage risk factors, minimizing the potential for budget overruns
Today’s cost estimating software delivers up-to-date cost data for better planning, helping calculate construction costs accurately and saving both time and money.
Enabling Stakeholder Confidence and Informed Decisions
A trustworthy cost estimate does more than win a job. It holds the construction project team together through every phase of the construction process.
From owners to subcontractors, when everyone trusts the numbers, project management works more smoothly, and issues are solved rapidly. DG Jones & Partners highlights how strong estimates support risk management and build lasting trust.
But a good construction estimate isn’t static. Effective estimates remain living documents throughout the project lifecycle, tracking actual project costs against budget, as The Constructor explains. This process ensures performance checkpoints and flags overruns before they jeopardize the total project cost.
With precise data, you can expect:
- Owners to confidently assess project feasibility and make informed investment decisions
- Contractors to staff jobs and plan work based on real construction costs and schedules
- Project managers to detect and fix emerging budget issues swiftly
Take cost estimating seriously, and you’ll see less guesswork and more honest communication about project costs. This shift benefits every stakeholder.
Construction Cost Estimation Fundamentals
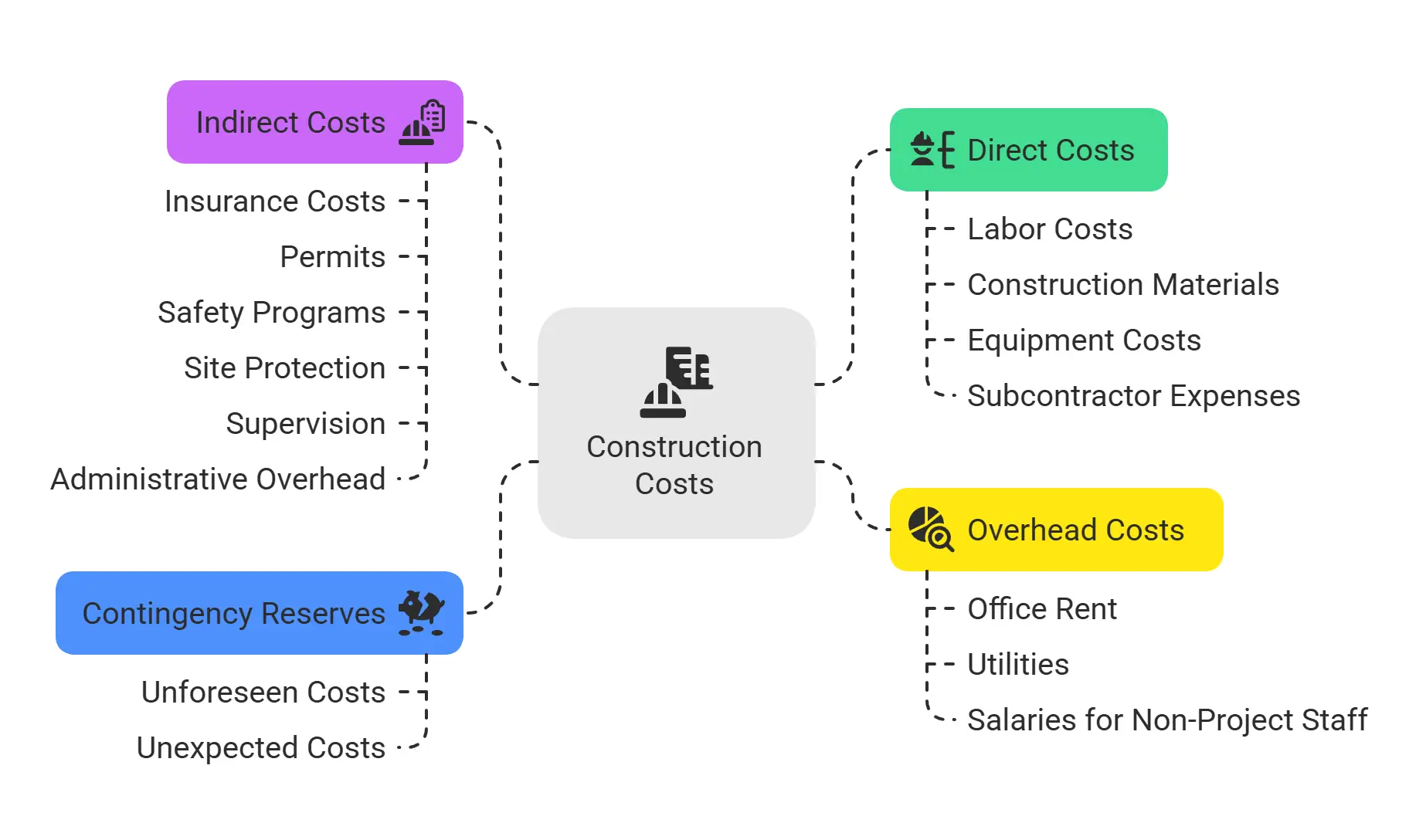
Key Components of Construction Costs
Construction costs cover direct costs and indirect costs: both must be captured to provide a more refined cost estimate and realistic budget.
- Direct costs involve resources linked right to construction activities, such as labor costs, construction materials, equipment costs, and subcontractor expenses.
- Indirect costs include insurance costs, permits, safety programs, site protection, supervision, and administrative overhead.
- Overhead costs are the fixed expenses a construction company incurs regardless of the project, for example, office rent, utilities, and salaries for non-project staff.
- Contingency reserves are set aside to handle unforeseen costs.
Estimators must account for as many influencing factors as possible, including topography, site conditions, scope, and all cost categories, to get as close as possible to the actual costs.
Types of Cost Estimates in Construction
There are five main types of construction cost estimates according to the American Society of Professional Estimators. Each category helps define the stage and accuracy of a construction cost estimate and supports informed decision-making for the construction industry.
1. Order of Magnitude Estimate
Also called the conceptual estimate or magnitude estimate, this is used at the earliest stage when project design is not yet available. It draws from historical data, past projects, and cost indices to provide a rough guide to construction costs, typically within ±20-30% accuracy. The goal is to assess initial feasibility and define early project scope.
2. Schematic Design Estimate
When schematic designs are ready but detailed plans are not complete, a schematic design estimate, sometimes called a preliminary estimate, offers better clarity about the construction process, material and labor costs, and time frames. This step is essential in narrowing down project costs and shaping resource plans.
3. Design Development Estimate
The design development estimate is built once the initial design is completed and more detail about construction specifications, quantities, and materials is available. This estimate refines the total cost, reflecting current market material and labor costs, and supports budget allocation and scope adjustments.
4. Construction Document Estimate
This occurs once detailed blueprints and construction drawings are available. Because this estimate is built from final design documents and actual quantities, it yields a more refined price estimate, which is crucial for budget control and financial approval.
5. Bid Estimate
The bid estimate is the final in-depth estimate before the project goes to bidding. It gives a line-by-line breakdown of construction costs based on construction estimates, supplier pricing, and labor rates. This is what contractors use to prepare construction estimates for submissions to owners.
Summary Table: Categories of Construction Estimates
Construction costs are also grouped as design estimates, bid estimates, and control estimates, each serving specific project management needs.
Key Estimating Methodologies
Choosing an estimating methodology is as crucial as the numbers you generate. The method you pick should match your current phase and the information on hand.
Analogous Cost Estimating
When details are still coming together, analogous or historical data-based estimating works well. Construction cost estimators look at previous projects with similar scope and use their incurred costs as a starting point.
This method is suitable when:
- The full scope is not defined
- Only limited technical documentation exists
- Early investment or funding approval is needed
AS Estimation & Consultants notes that adjusting for unique project conditions, such as site, region, and complexity, is critical. Reliable databases and a deep understanding of your past projects enable a more accurate estimate construction costs.
Unit Cost Estimating and Its Role
When more details are available, the unit cost method is the go-to technique. Here, every task is broken down to units, such as square feet, cubic yards, or labor hours, and priced out using up-to-date data.
The unit cost approach enables:
- Precise breakdown of material and labor costs
- Transparent, detailed estimates for owners and project managers
- Easier updates as prices and quantities change
Buildern points out that current cost libraries are essential here, as market shifts can quickly change both unit cost and overall construction costs.
Order of Magnitude, Control, and Detailed Estimates
- Order of magnitude estimates work with minimal data, setting a ballpark figure.
- Control estimates act as benchmarks after scope definition, enabling comparison of planned versus actual costs.
- Detailed estimates use completed construction documents and real-time supplier/labor pricing for the most precise budgeting possible.
Construction Document Estimate and Bid Estimate
Utilizing detailed design documents, contractors can produce accurate and competitive bid estimates. These are vital for securing work and ensuring projects are won profitably.
Indirect and Overhead Costs in Estimating
Every construction estimate must include indirect costs and overhead costs. These may cover supervision, equipment maintenance, temporary site facilities, and insurance cost money. Omitting them leads to major budget issues later.
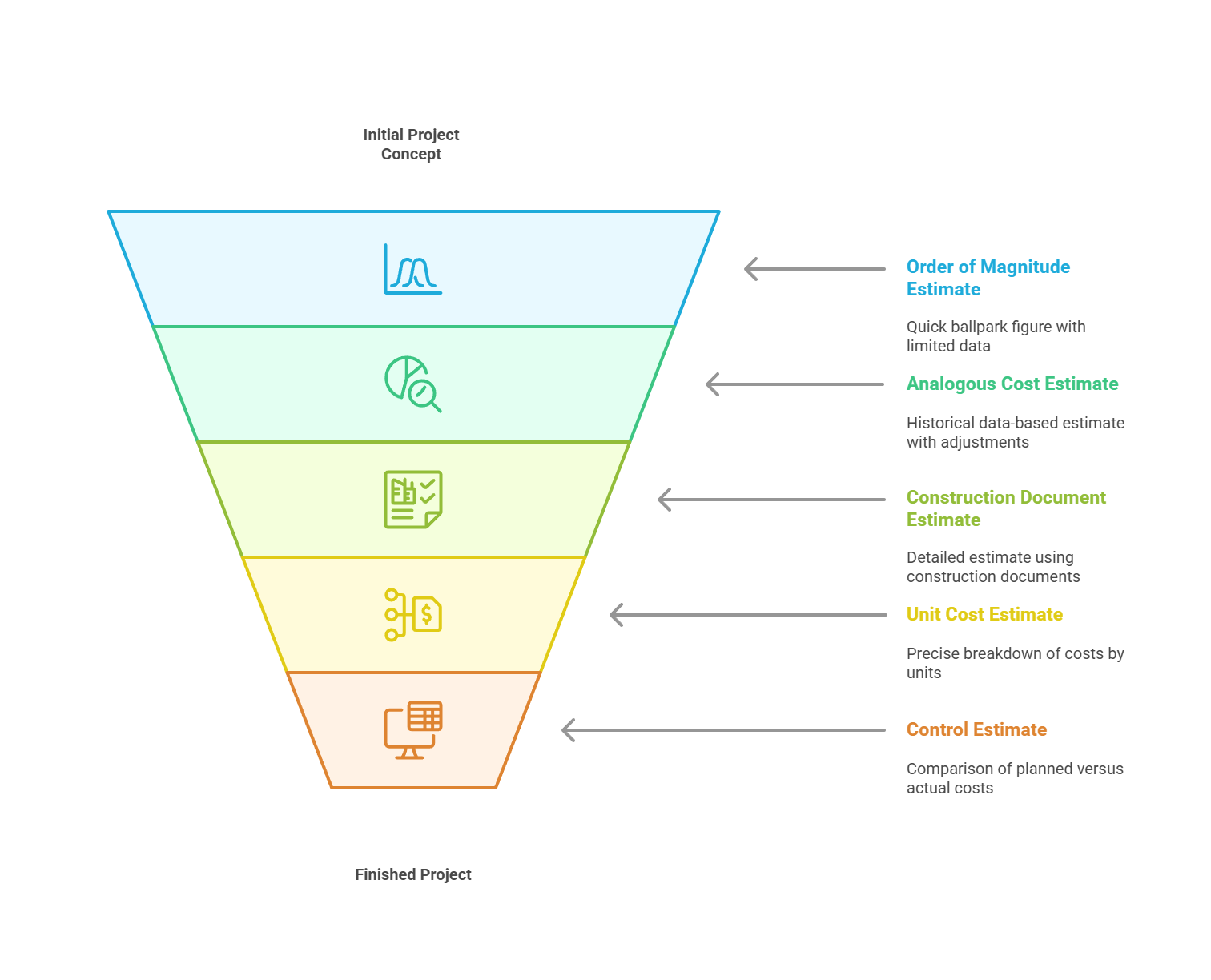
The Construction Estimating Process: A Step-by-Step Guide
An accurate cost estimating process delivers much more than a number on a spreadsheet. It drives decisions, schedules, and outcomes across the entire construction industry. Precision and discipline are key at every stage.
1. Early Planning and Scope Definition
Estimation begins at the idea phase, often before any physical work starts. Project planning involves:
- Clearly outlining the construction project goals and requirements
- Engaging with architects, engineers, and stakeholders early
- Ensuring project scope aligns with the budget and timeline
2. Conducting Thorough Site Investigations
Site visits are essential. Conducting a site visit before estimating helps outline environmental and logistical aspects impacting expenses. Zintego warns against relying solely on drawings. Topographical challenges, soil quality, access, and site conditions all profoundly affect construction costs.
3. Gathering Construction Paperwork and Specifications
Construction documents, such as blueprints, plans, and specification sheets, are the basis for detailed estimates. Construction specifications provide exact requirements for materials and workmanship, serving as the groundwork for accurate calculations.
4. Performing Quantity Takeoffs
Accurate quantity takeoffs are the backbone of any cost projection. Estimators ensure precise calculation of every required material and task, often using digital takeoff tools.
With BIM takeoff modules and construction management software, measurements pulled directly from current models or construction documents reduce human error and missed items.
5. Calculating Material and Labor Costs
Estimating material costs involves determining quantities needed and obtaining supplier pricing. Material costs vary by region and time, making real-time data and vendor outreach important.
Determining labor costs means breaking tasks down into labor hours, factoring in wage rates, productivity, required skills, and regional variations. Underestimating labor costs is a common pitfall.
6. Assessing Equipment Costs
Equipment costs, such as purchase, leasing, maintenance, and operation, are tabulated based on project needs and expected durations. Construction equipment choices can impact both direct and indirect costs.
7. Including Indirect Costs
Indirect costs stand apart from specific trades or tasks but are essential to capture. These include insurance costs, permits, administrative overhead, utilities, security, and supervision. Assign overhead and indirect costs deliberately to ensure complete project costing.
8. Allowing for Contingencies and Risk
Contingency reserves account for unplanned costs: hidden construction site conditions, supply chain disruption, or even weather. Risk management is critical. Anticipating potential complications or market fluctuations improves cost estimation and protects profit margin.
9. Compiling and Reviewing the Cost Estimate
All assumptions, exclusions, and calculations should be documented. Reviewing the base estimate with all stakeholders ensures every aspect is captured, and fosters collaboration for improved accuracy.
The estimator continuously updates construction costs as project conditions evolve, scope changes, or new information arises.
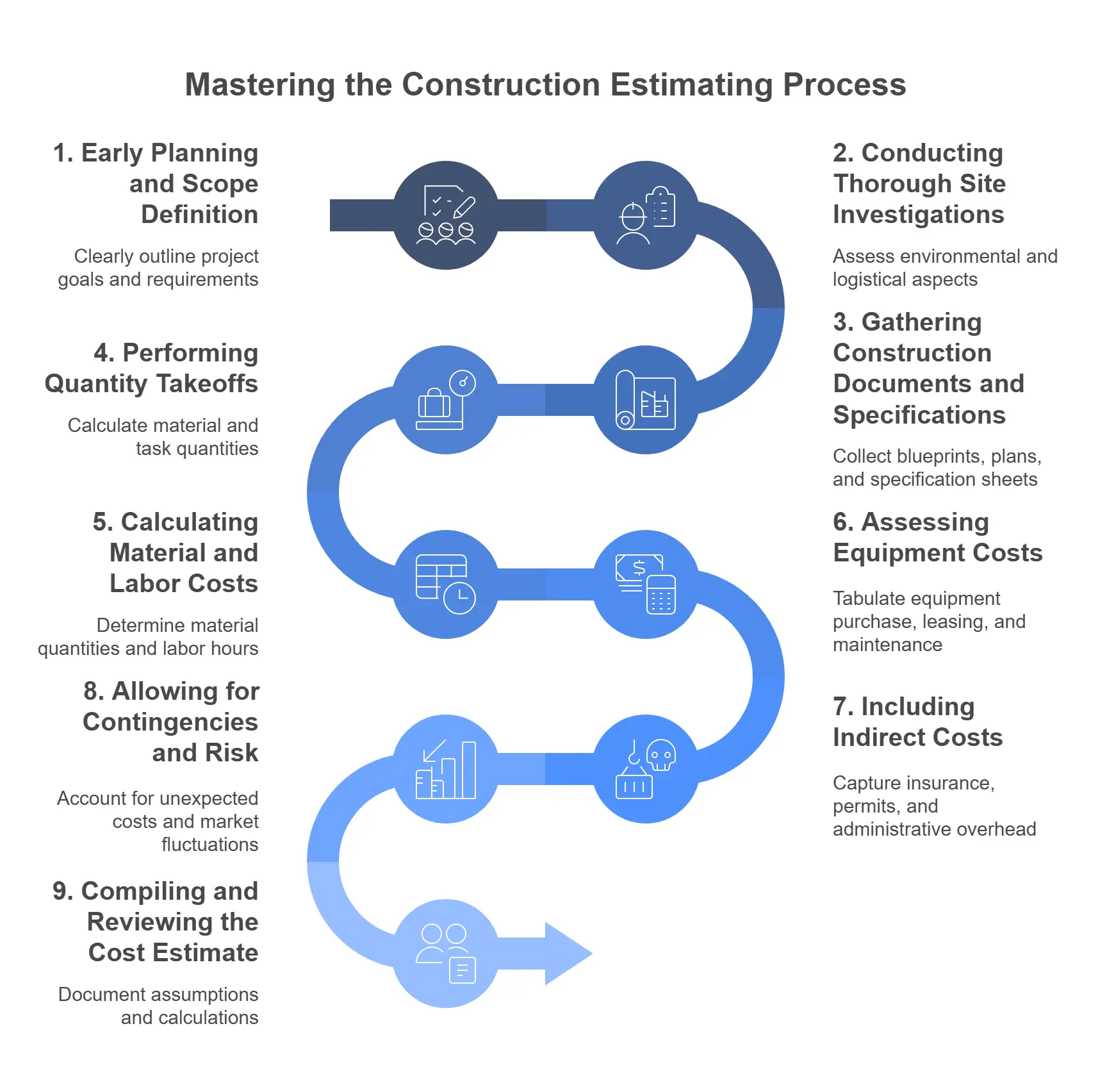
Leveraging Construction Estimating Software for Greater Accuracy
The Power of Construction Estimating Software
Modern cost estimating software helps improve the speed and accuracy of cost estimates. Features include:
- Automated cost calculations and digital takeoffs, reducing human error
- Storage of data from past projects for future reference
- Streamlined workflows and reporting, supporting competitiveness and reducing unexpected costs
- Cloud-based platforms promoting collaboration and effective project management
- Integration with project management software for better project control and project costs tracking
Autodesk highlights that advanced estimating software takes on repetitive math and data entry, freeing up time for valuable analysis and decision-making.
Nomitech’s CostOS is an example of an all-in-one software solution designed for complex construction projects.
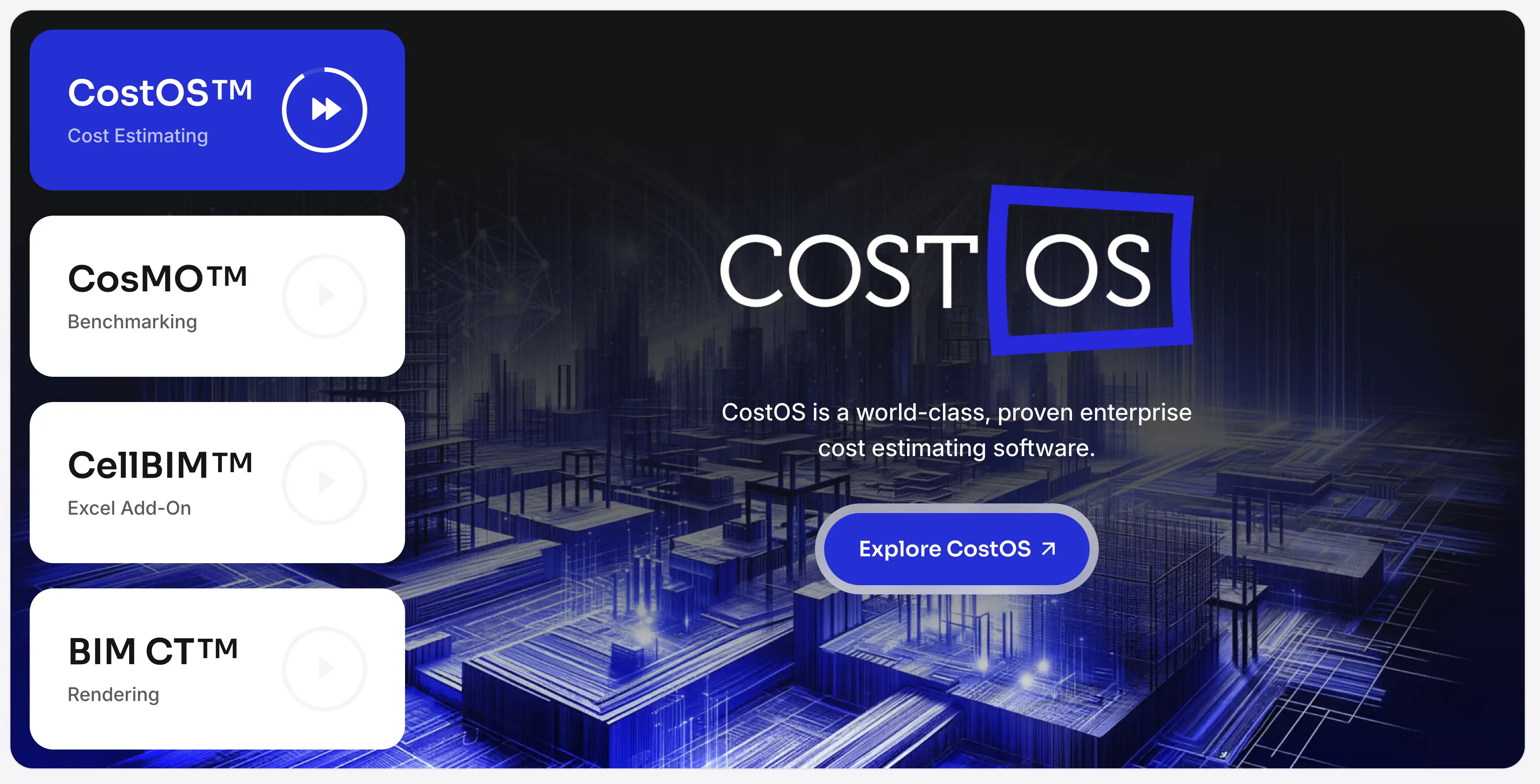
BIM for Integrated and Visual Cost Estimates
Building Information Modeling (BIM) transforms cost estimation by tying costs directly to a 3D project model. This integration enables:
- Efficient extraction of quantities directly from models, rather than static plans
- Real-time updates of cost estimates as designs change
- Clear visualization of project scope for stakeholders
A powerful BIM rendering engine helps teams spot missed items and scope gaps. With BIM, construction cost estimates always reflect the latest design, supporting more accurate cost forecasting and improved collaboration.
The Role of Historical Data
Historical recors are key for contractors to rely on for estimating construction costs. Past project outcomes, market trends, and vendor pricing give context, validation, and realism to both conceptual and detailed estimates.
Estimating Software and Project Control
Using estimating software alongside project management tools offers complete project oversight: tracking scope changes, managing actual costs, updating stakeholders, and facilitating risk control.
Construction Cost Estimation: Ensuring Accuracy and Avoiding Pitfalls
The Risks of Inaccurate Construction Cost Estimates
Failure to factor in risks, uncertainties, or precise takeoffs can lead to inaccurate construction estimates.
Frequent cost fluctuations in material and labor costs, weather changes, and even overlooked insurance costs can wreak havoc on project budgets and profit margins. Good estimation mitigates unexpectedly high expenses and protects stakeholders.
How Construction Cost Estimators Overcome Challenges
- Anticipate potential complications
- Collaborate with architects, engineers, and vendors
- Use historical data, construction estimation software, and ongoing review to validate figures
Integration of Real-Time Data and Scenario Analysis
Live market data on direct and indirect costs helps keep construction cost estimates current, minimizing the chance of budget overruns. Powerful scenario analysis tools, available in advanced estimating software, allow teams to test the impact of price changes, delays, and other variables before problems arise.
Teams who prioritize accuracy also consider sustainability metrics, such as CO₂ impact, providing added value to owners and clients.
Indirect Costs, Overhead Costs, and Contingency Reserves
Every budget requires a clear accounting of overhead and indirect costs. These often-overlooked items can push total project cost above the approved limit if not anticipated. Make contingency planning routine to manage the unavoidable unknowns.
Essential Facts for Accurate Construction Cost Estimation
- Accurate estimations enable on-time and on-budget project delivery
- Reliable construction cost estimation prevents budget issues and financial losses
- Both direct and indirect costs must be included for a complete estimate
- Contingency funds and risk management protect project budgets
- Early, frequent, and thorough estimation supports better contracts and decision-making
- Strong historical data and modern estimating software lead to the most accurate cost forecasting
Frequently Asked Questions About Construction Cost Estimation
What types of construction cost estimates are there and when are they used?
There are five main types of construction cost estimates: Order of Magnitude, Schematic Design, Design Development, Construction Document, and Bid Estimate.
Use order of magnitude and schematic design estimates early for feasibility checks, then develop detail with design development and construction document estimates. The bid estimate is your final, most precise submission before seeking contracts.
How does estimating software improve accuracy and efficiency?
Construction estimating software automates calculations, stores historical data, manages digital takeoffs, and integrates with project management platforms. This reduces errors, speeds up the estimation process, and ensures construction estimates are both accurate and consistently updated throughout the project.
What is the role of Building Information Modeling (BIM) in construction cost estimation?
BIM allows estimators to draw costs and quantities directly from live, comprehensive project models. Adjustments made to the design are immediately reflected in the construction cost estimate, reducing missed items and increasing cross-team collaboration.
Why are site investigation and quantity takeoff important?
A comprehensive site investigation reveals environmental and logistical factors that could drive up costs. Detailed quantity takeoffs ensure that every material, labor hour, and piece of equipment is accounted for, cutting down on unexpected costs and ensuring that budgets hold up in the real world.
How does using real-time data help prevent budget overruns?
Using live data for material, labor, and equipment costs means estimates reflect current market realities. Scenario analysis features in advanced estimating software allow teams to quickly model the impact of changes and prevent costly surprises.
What should be included in a comprehensive estimate?
A full estimate should include quantities, detailed line items for materials, labor, equipment, subcontractor fees, all indirect and overhead costs, contingencies, insurance costs, and clear documentation of assumptions and exclusions. This level of detail allows for competitive and reliable price estimates.
Best Practices for Effective Construction Cost Estimating
Always Start Estimation Early
Estimators must begin as soon as possible, ideally at the concept phase. Early estimation helps shape scope, align budgets, and set realistic expectations.
Collaborate and Communicate
Consistent collaboration with owners, designers, project managers, and suppliers ensures assumptions are accurate and all cost drivers are transparent.
Make Use of Modern Estimating Tools
- Adopt cloud-based and AI-enabled construction estimation software to streamline processes
- Use BIM to integrate quantities and costs with dynamic design changes
- Rely on current historical data for all estimate categories
Regularly Update and Review Estimates
As scope, design, or market conditions shift, adjust all related cost estimates. Continuous review and adjustment prevent overruns and keep all stakeholders updated.
Document Everything
Include all assumptions, exclusions, and supporting data for every cost estimate. Transparency builds trust and allows future re-evaluation if conditions change.
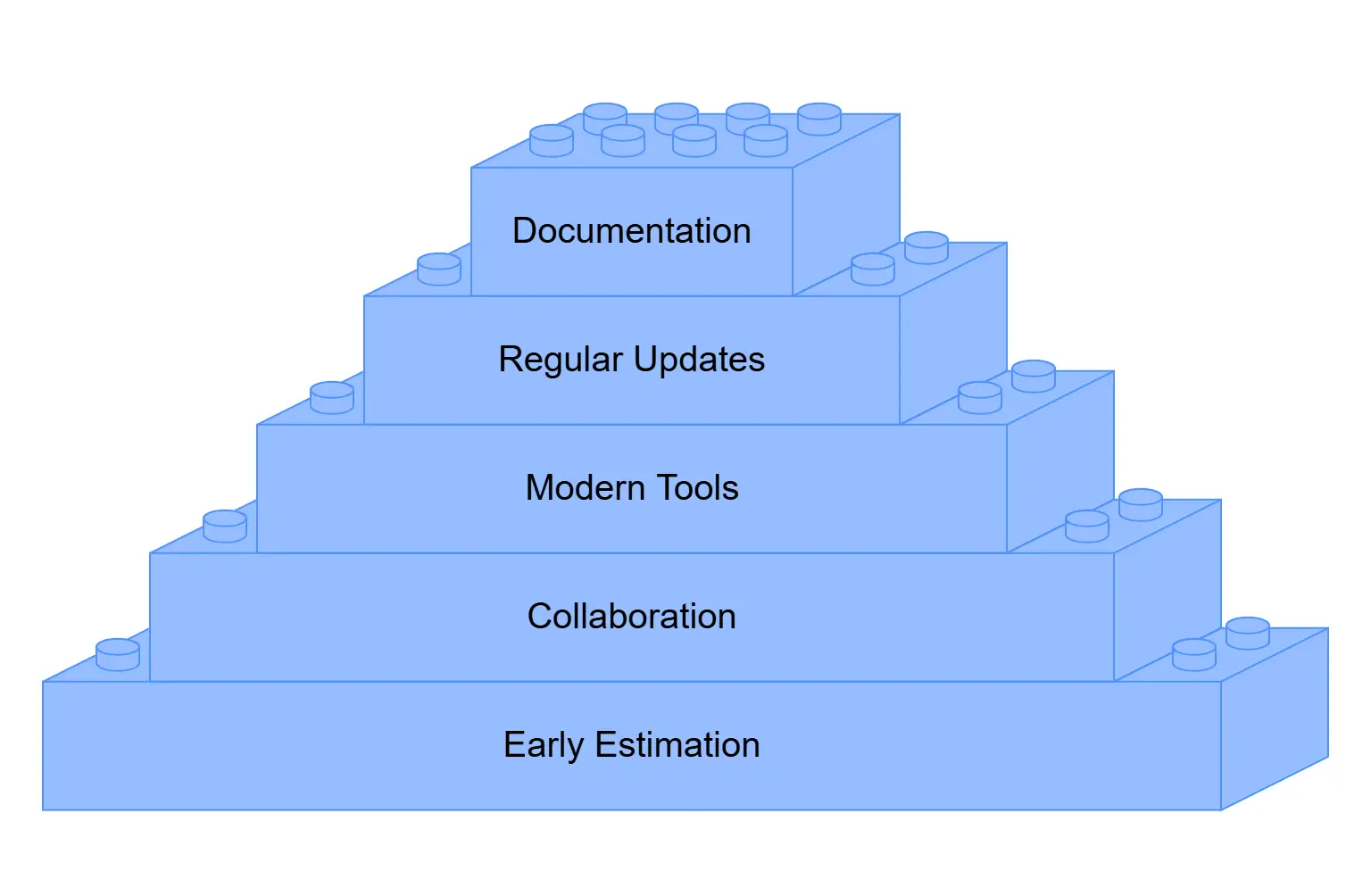
Conclusion
Nailing down accurate construction cost estimation is what separates winning, profitable construction teams from the rest. With the right blend of hands-on process, proven methodology, and next-generation construction estimating software, you can control known costs and deliver even the most complex building projects on time and on budget.
Now is the ideal moment to upgrade your cost estimating workflow and give your next construction project its best chance for financial success.
Ready to Take the Next Step?
If you’re ready to discover how construction estimating software and modern tools can improve your next project, explore Nomitech’s full suite or connect with our team for guidance on the solution that fits best.